Can You Use a Ceramic Kiln for Glass
Ceramics and glass go hand in hand because silica, the primary component of glass, is typically found in regular glazes. Your pottery may produce the most astounding outcomes when you incorporate glass beads. The light will reflect off the glass after your piece has been coated, giving it the appearance of a priceless jewel.
The colors, which are so strong and vivid, really capture the eye. Any ceramic piece you create using glass will undoubtedly be a little show-stopper. This technique is what they mean when referring to “warm glass,” if you have heard that term.
The magic of pottery is created in kilns. Your unfinished work of art becomes a finished work of art during the firing process, which transforms clay into ceramics. Early kilns were simply fired over a hole in the ground, but as technology, advanced, more complex ceramic kilns were made. The appearance of a ceramic object depends greatly on how it is burned. Firing is a craft in and of itself, requiring a lot of experimentation and an open mind.
What is Ceramic Kiln?
Are you prepared to advance your pottery-related passion? Selecting a kiln is probably a top consideration if you’re interested in opening a home studio. As you start your search for the best ceramic kiln, there are numerous factors to take into account.
To make the process less intimidating, we’ve put up a guide addressing the key factors you’ll want to examine. We’ve included our suggestions at the conclusion to make it easier for you to pick a kiln that best suits your requirements and interests.
Ceramics is the art of shaping clay minerals, which are then rigidified via the use of various heating techniques, into forms that are utilitarian and/or aesthetically pleasing. The majority of people on earth are familiar with clay in one way or another, but it is helpful to have a fundamental awareness of its qualities, the different kinds of clay that are accessible, and basic forming techniques before starting to work with clay.
Types of Ceramic Kiln
Electric, gas, and wood kilns are the three most popular varieties. Probably the most popular kind of kiln used in ceramics is the electric kiln. Small pottery operations can use them because they are reasonably priced and small ones can plug straight into a 120-Volt wall socket.
These kilns always operate in oxidation, which means that oxygen is present in a well-regulated atmosphere. This produces consistent results with glazes. For a potter who wishes to duplicate their work, this control is crucial.
Gas kilns use natural gas as fuel and burn in reduction, which prevents oxygen from entering the fire during firing. Although the effects of reduction firing can be unpredictable, they often provide deep, earthy colors. Since uniformity is difficult to maintain, gas kilns are best suited for unique designs.
Pottery has been produced for thousands of years in wood-fired kilns. if you want to know how to bake the clay artifacts with firing kiln then read this post for better understanding. They need a lot of manual labor because the wood needs to be constantly stoked and refueled to maintain a high temperature. Fire burning in a wood kiln can take three times as long as it would in an electric or gas kiln, and it must be watched constantly. As the pieces are fired, the wood ash that falls on them causes the kiln to produce its own glaze. Many potters think the extra work is worthwhile for the distinctive outcomes.
Additionally, a few other kinds of specialist kilns exist that yield particular surface effects. Stoneware items most frequently have a rough glaze created by salt kilns, sometimes called soda kilns. When salt is added during the last firing stage, this occurs.
Heat causes a chemical reaction in the salt that results in a glaze-like residue that resembles an orange peel. Additionally, this glaze gets all over the kiln, which could shorten its life.
Another specialist kiln that produces a particular finish is the raku kiln. When the raku pottery is blazing, it is removed from the kiln using tongs. The sculpture is placed in cold water after cooling to produce a crackling effect.
How to Use Ceramic Kiln for Glass?
The best part about making this form of art is that you don’t need anything special to produce it; you can use reasonably inexpensive glass and fire it in your standard ceramic kiln because you can adjust the kiln’s temperature.
Glass kilns burn from the top down, often to produce an even heat on flat glassware, whereas ceramic kilns fire from elements around the kiln to heat the objects uniformly. This is the major distinction between a glass kiln and a ceramics kiln.
However, there are several things to keep in mind, namely the fact that glass expands when heated and shrinks when it cools, so you’ll need to make sure it has enough room in your creation to do both in order to prevent the possibility of it splitting at any point during the fire.
The easiest place to start when combining ceramics and glass is with something straightforward, like a bowl with a base that is wide enough for the glass to melt and pool into. Take care, not to overuse glass in your creations. Here, a little goes a long way, and you don’t want to run the chance of your ceramics cracking due to the changing state of the glass.
You can use the glass in a variety of ways when doing your work. You can first place it on top of the glazed work. You can glaze your piece, remove some of the glazes in specific areas, and then add the glass to achieve a distinct effect.
There are a lot of things to think about with this because the sort of glass and clay you choose can greatly influence the outcome. Before firing your main pieces with glass, it is advisable to test out your clays and a small glass mixture on a few test tiles.
With this kind of work, the possibilities are really limitless. Check out the amazing ceramics of Steven Branfman for some inspiration. He coats the outside of his pieces with the most fantastic textures by rolling his ceramics in crushed glass and firing them in a Raku method.
Useful Glass Types
Similar to clay, glass undergoes state changes depending on the materials it is constructed of at various temperatures. Standard soda lime silica, the most prevalent type of natural glass, melts at 1500 C (about 2700 F), according to Lakeside Pottery, whereas pure silica requires fluxes to melt at a lower temperature. It’s best to start off firing the task cautiously.
Using glass beads is a stylish approach to work with ceramics and glass since the colors are vibrant and they are a good size and soft circular form. Due to the temperature at which it melts and for safety concerns, resist the urge to utilize broken glass.
Conclusion
You see, even in modest ways, you can add the beauty of glass to your art room with a little planning and research. You could come across some widespread myths about utilizing glass in ceramic kilns along the way.
Wow, that’s a lot of details! I hope it opens up for you a wider range of options for your art curriculum. If you’re anything like me, it’s worth the extra effort to find a unique art project to offer students so they may experience the “WOW” effect. The triumph is art.
if you want to know how to do oil painting on glass then read about it in this post in detail.
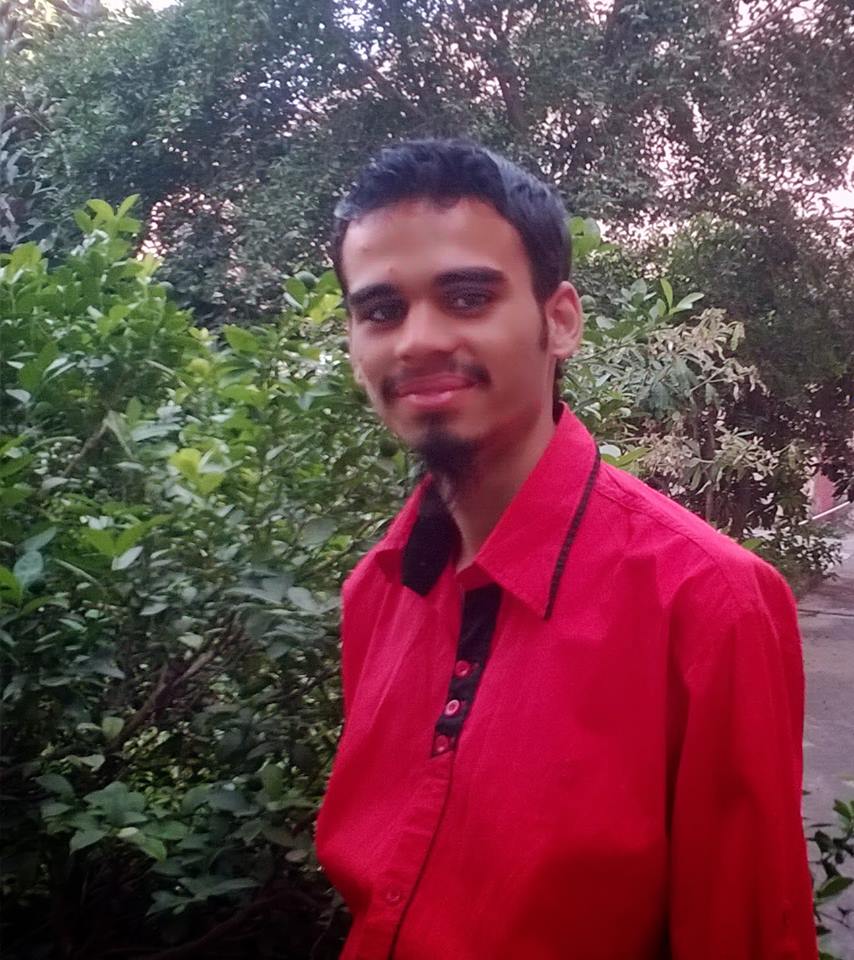
Being associated with art and craft field since decades as a hobbyist and life long learner has given me an opportunity to learn many new things related to art, craft, paints and pottery which i am trying to share with your guys on this website. I have expertise of being professional painter and potter for the last 20+ years
I have learned mind blowing cool tips and insights which makes me a person with ability to improvise and come up with creative ideas and solutions to make stunning and impeccable art pieces of all types which are adored by people across the globe on this website and other platform.