What is Raku Pottery: Detailed overview with tips
Raku is a low-firing method that was inspired by traditional Japanese raku. Western-style Raku usually involves taking the pottery out of the kiln at a bright red temperature and placing it in containers with combustible material. The containers are sealed once the materials have ignited. The intense reduction atmosphere produced by this process affects the color of glazes and clay bodies. This thermal shock can also cause cracking, called crackling because it’s deliberate. Buddhist life influenced the Japanese original raku style, especially the tea ceremony.
What is Raku pottery?
Raku is a Japanese technique for making a unique bowl. This technique has been used in Japan for many years and is closely related to Japanese tea ceremonies. Raku involves removing glazed ceramics still hot from the kiln.
The ceramic is placed into an explosive substance, such as sawdust or paper. The glazed item is then forced to cool quickly, where the oxygen on the surface is depleted. This method can produce an intense reaction that produces a mixture of colors within the glaze. It is possible to do this without using a glaze. This will produce a matte or black color. The intense heat or temperature change also causes cracking. This is known as “cracking” and is done intentionally.
Roku is a process that can be done by hand without a wheel. Raku creates unique clay items because you have no control over the process and never know what will happen. Raku pottery is made using only natural elements. Earth is used to create the object, then fire in the kiln. The item can be cooled down in either air or cold water.
In Western and Japanese culture, Raku is a low-fire method. Western Raku is made of stoneware clay and is bisque-fired to 1830 degrees Fahrenheit. It is possible to use an electric kiln, but this is not recommended. A gas kiln for Raku kiln would be better.
Raku Pottery Originated In Japan
In raku history, it is mentioned that the Zen Buddhist Masters used raku in their tea ware. This dates back to the 1550s. Zen Buddhist Masters used this method to create their ceramics. It is well-documented that raku ware embodies many aspects of Zen philosophy, including its simplicity and naturalness.
The Raku technique had a single purpose- to promote beauty. Raku is shaped by hand, not on a wheel, as this is what the potters prefer. Each Raku piece is unique and beautiful.
Have you ever watched a Japanese tea ceremony in its traditional form? Raku is used. This art form was appreciated by the tea master for its beauty and simplicity. Raku ceramics have been highly sought after in Japan for centuries because of their beauty. Raku pottery is often regarded as Zen.
Raku literally means ‘happiness in the accident.’
Traditional Japanese Raku vs Western Raku
The traditional Japanese Raku is different from Western Raku. Western Raku is likelier to use bright metallic colors, whereas Japanese Raku prefers neutral colors such as blacks and browns.
There are two main types of Raku in Japan: Kuro (black) and Aka(red). Aka is cooler when they light the kiln than Kuro. It is the glaze maturing that makes a difference. Low melting glaze seals carbon deposits.
Western Raku is often avant-garde. Paul Soldner is an American ceramicist credited with Raku’s popularity in the West.
Raku in the West is not associated with Japanese tea ceremonies, while Traditional Japanese Raku strongly associates with the Zen tea ceremony. This is a four-hour spiritual process.
Raku Pottery Techniques and Processes
The Raku method is faster and can be completed in one to two hours instead of a whole day. Normal temperature changes are made gradually and with care. Rapid cooling can occur in crackpottery. Glazing your item is the first step in Raku pottery. Glazes are made with a low melting temperature; only a thin coating is needed to achieve the desired result. We will now look at the Raku process in more detail.
Raku Firing Technique
The pottery is heated quickly in the Raku method. Raku firing cycles are short, depending on the glaze and kiln used, and can last only 15 to 20 minutes. Using tongs, the ceramic object is removed and quickly cooled in air or water. The item can be removed once the glaze stops bubbling and looks glassy.
You should protect the pottery and yourself when removing it from the kiln. Western methods involve a reduction after firing, in which you place the pottery item into combustible material. This will produce a lot of smoke. Here are some suggestions on how to use these materials.
- Sawdust
- Paper
- Woodchips
- Pine Needles
- Straw
- Nutshells
- Dry Leaves
Another idea is a technique used in Eastern Europe where flour, water, and yeast are mixed three days before use. After bisque-firing, the item is removed and placed into the flour, water, and yeast mixture. It is then soaked in a solution of water and yeast. In Western Raku, the pottery is bisque-fired first, making the clay more porous and durable. Raku firing can take between 30 and 90 minutes.
Clay Shapes and Textures
It is recommended to use a specific Raku clay, as it is resistant to thermal shock and doesn’t shrink. Stoneware is used for traditional Raku because it is more durable and less porous than earthenware. Any type of clay can be used, preferably with higher grog content. Grog is a grainy material added to pottery to give it certain properties. It can improve thermal shock resistance and reduce cracks as well as shrinkage.
The clay ball is flattened to a thick disc, and the palms shape the edges. After the clay has dried, it is trimmed before being covered with glaze. This results in a bowl with straight sides, not too wide, and a narrow bottom. A Raku ceramic can take any form, but you must consider the extreme temperature fluctuations and pressure that the clay is under. Items that are thin and evenly made tend to last. Here are some shapes that will withstand the process.
- Curved shapes
- Round orb shapes
- Vertical sculptures and pots
The same is true for items with too many fine details or those that vary in thickness. Raku-fired pottery that is plain and smooth looks the best. The Raku finish can be affected by adding textures or fine details.
Some potters use different techniques or textures. Horsehair Raku, for example, is a unique idea. You can use horse hair or other materials such as human hair, dog hair, or feathers. The combustible material will leave a mark, which is then infused into the surface of the ceramic item, creating a unique design. This technique works even better if the pottery has been burnished. Burnishing is a process that polishes the pottery to a shine without a glaze. Some use terra sigillata, a super-fine clay slip, to give a soft shine before burnishing.
Top Glazes
Since raku is low-fire, any low-fire glazing should work, whether purchased in a store or made yourself. Raku firings usually reach temperatures between cone 010-06 range.
Raku can be embellished in many ways, but not all require glazing. Western potters rarely use glaze for Raku because of its toxicity.
Raku can use other metals with different effects as glazes. Low firing temperatures are a problem for Raku and its glaze. Low temperatures cause the glaze to not adhere as well to clay.
Kilns
Various raku-kilns are available, all designed specifically for the raku-firing method. But skilled potters can make their own raku kilns from dustbins.
The item will typically be bisque-fired first, then raku-fired.
The glaze is applied, and then the raku is burned. If you throw it into the fire, you can fire raku pottery in just 15 to 20 minutes.
Raku firing is usually much faster than regular firing. For raku, your ceramics must be placed into combustible materials, like sawdust.
Be prepared for a lot of smoke when raku-firing.
Safety precautions
Here are some safety tips for Raku firing. When dealing with high temperatures, it is essential to be prepared. Depending on the reduction method, Raku pottery can also produce a lot of smoke. First, consider a respirator that filters out fumes and particles. It is best to use specially designed Raku metal tools to remove the ceramic.
- Wear a face shield or combination respirator/face shield to protect your face.
- Avoid wearing sandals and open-toed shoes. Instead, opt for closed sneakers or booties.
- Cotton is the best material to wear since synthetics are highly flammable.
- Wear long sleeves to protect your arms.
- You can also use a welding coat if possible.
- Wear flame-resistant gloves to protect your hands.
- Keep a fire extinguisher nearby.
How is Raku Pottery Different?
Clay is the first thing we need to discuss when comparing Raku with other types of pottery.
While most artists use raku clay for their raku pottery, any type of clay can be used. Special raku pottery clay produces the best results. Raku clay is generally resistant to thermal shock and shrinkage. The right glaze is also essential in creating your raku. It should have characteristics that react well in a raku fire.
The unique firing method is another important feature that sets Raku apart. The firing process is usually completed in 60-80 minutes. The clay is heated rapidly. Second, the clay, often red hot, is removed from the kiln.
Raku pottery cooling techniques are also unique. Japanese masters traditionally took raku pieces out of the kiln while they were still very hot and allowed them to air-dry. This method can produce stunning results. You may see metallic or cracked surfaces.
Modern methods are used because air drying takes a long time. Modern techniques submerge the pots in cold water. Thermal shock can occur more often. This cooling method is not based on traditional methods and is more modern.
Explore the Unique Qualities Of Raku Clay – An Overview
Raku clay can be used for pottery and sculpture. It is known for its unique properties, which makes it perfect for a wide range of applications.
Raku clay is an earthenware, low-fire clay typically fired between 1700 to 1900 degrees Fahrenheit. This porcelain-like clay is not waterproof and can easily be scratched or dented. It is very absorbent and shrinks when it’s fired.
Raku clay comes in many colors, from light cream to dark brown. The glaze used to cover raku clay can be glossy or colored with different pigments. The glaze is applied to the clay and fired again after it has been fired.
Raku clay can most commonly be used to make decorative items such as masks, figurines, and sculptures. The clay is also used for raku-firing, a method in which the clay in a kiln is quickly heated and then rapidly cooled. The finished piece will have unique textures and patterns.
Raku clay can be used for both wheel-throwing and hand-building. The clay can be used to create both functional and decorative items. Both amateur and professional potters love it because it is easy to work with.
Is Raku Pottery food safe?
Raku pottery cannot be used as food without being properly sealed. The quick-firing method leaves ceramic pieces fragile and porous.
It takes between 8 and 12 hours for a regular electric or gas kiln to fire pottery properly. The firing process of Raku is quick. Raku pieces are typically fired between 30 and 90 minutes. The temperature of raku firing is also much lower. The low temperature and short firing time prevent the glaze and clay body from maturing. This leaves the clay porous.
The rapid temperature changes when the pottery is removed from the kiln into the air can also cause the surface to crack or be rashed. This is not a good feature for dinnerware.
Sealing raku pottery can make cups and bowls suitable for liquids and dinnerware.
How can I preserve the beauty of Raku pottery?
It is important to note that not all pieces of raku pottery require the same type of preservation. The pieces made of low-temperature ceramics are more likely to break down if exposed to liquids or water for a long time. It is best to use them only as serving pieces or drinking vessels. If you can’t imagine not using raku ceramics for decoration, protecting the piece from liquids or extreme temperature changes is important.
How valuable is Raku pottery?
Raku pottery is usually less expensive than traditional ceramics. Still, prices can vary depending on the size of the piece, how it’s designed, and whether precious metals such as gold or silver are used. Shirako Tamaya and Teshio Tamaya glazes are more expensive than traditional raku ceramics. This is because they require harder-to-find materials, while the process requires multiple attempts to achieve the desired result. Most Raku pots don’t have any designs unless you’re looking for something specific, like serving drinks or food.
Raku Pottery Today
Some Vietnamese potters are currently working on replicating the work of Japanese masters in raku ceramics while adding their own Vietnamese twist to the technique. This allows them to do small runs of products for brands in the home décor and furnishing industry to be used in their collection.
Here are some fun facts about Raku ceramics, glazes, and more:
- Raku glaze is fired four times.
- If the vase is to be able to hold water, a thin layer of silicone will be applied inside.
- Raku Glaze is a natural metallic glaze, unlike any other glaze; after several years, the color of a raku glaze may darken due to oxidation. The colors may disappear if they come into contact with harsh chemicals.
- Raku is a rough, rustic glaze. The product’s surface may not be as smooth or even as normal glazing.
- There may be small crackles on the surface of the glaze. This is normal.
- The Raku glaze reacts to heat and fire. As a result, each piece is unique and will have a different finish.
- The raku glaze is fired or removed from the kiln one at a time.
Tips for Successful Raku
Raku glazes are unsuitable for complex shapes or those with a lot of texture. Raku glazes are best displayed in simple forms and unhindered surfaces.
Naked Raku
This method only works if your pots are correctly prepared. Use a White firing body. When the pot has dried, it is best to burnish or polish a few layers of Terra Sigilata. The final surface should be shiny and smooth. Burnishing your regular clay without Terra Sig is also possible. As we are using a slip, it is not essential. However, it may help if you let the slip dry completely before glazing. The naked Raku technique is also called Slip Resist.
Copper Fuming
This technique is best used with nice bottle shapes. The best shapes are those with narrow necks and bellies. For some reason, flat items don’t react as well to fuming. Please bring a pot cover.
Copper Bling
The best results are achieved when the copper is partially reduced before it goes into the bins.
We like to turn shallow bowls and cup forms upside down to prevent oxygen from reaching the glaze during the reduction process. This gives us a shiny, blingy finish. It is best to keep surfaces uncluttered, but textures will also look great.
Saggar Firing
Pots are wrapped twice in Tin Foil, then fired at a specific temperature. We remove the foil saggars, peel back the foil, and let the pots cool. Once cool, spray them with clear lacquer.
Final Thoughts
Raku has been around for centuries. Since its creation, the raku has been subjected to many changes since its creation, particularly in Western countries. You can now make your own raku using readily available materials.
Safety precautions should be taken when using or making a raku. Raku is an excellent alternative to an electric kiln.
Frequently Asked Questions
What does Raku mean in ceramics?
Raku pottery is often associated with the Japanese Tea Ceremony. The term raku in Japanese means “enjoyment” and “comfort”; this pottery type is known for its elegant, simple designs. Raku pottery usually has a white body made of clay and is fired to a lower temperature.
What is Raku Pottery Better For?
The Japanese use Raku for their tea ceremonies. However, you can use it for only decorative purposes.
Raku is porous and fragile, so even the Japanese aren’t able to leave their tea for very long. If the glaze is overused, it can flake off in certain areas. Raku wares are beautiful but not meant for everyday use or food safety.
What Is the Purpose Of Raku?
Raku is used to heat the ceramics until they glow red. The piece will be removed from the raku quickly and cooled. It will either be oxidized or reduced by the cooling process.
If the piece is oxidized or reduced, the glaze will take on different colors.
Can raku pottery get wet?
Raku pottery is designed to be wet and exposed to liquids. They are made from clay, wood chips, and straw ash. These all work together to make them as durable as possible. They are perfect for serving drinks or food, but extreme temperature changes can cause them to break.
What safety precautions should I take with Raku Pottery?
Raku pottery is not as durable as traditional ceramics. They also do not adhere to harsh chemicals such as bleach, ammonia, or vinegar. Because raku ceramics are not usually fired in a traditional kiln, there is a risk of warping and breakage. Due to the possibility of breaking and warping, raku pottery should not be used for serving food.
Does Raku require glaze?
Raku can be decorated in a variety of ways, some without the need for glaze. Raku can be decorated with oxides or stains instead of glaze. Each has its own unique effect. Raku glazes are problematic because of the low firing temperature. It is suggested to use low-fire glazing because of the low temperatures. if you are interested in knowing how to remove or reduce pottery glaze if and when required then read about its simple and easy to follow process in this insightful article now.
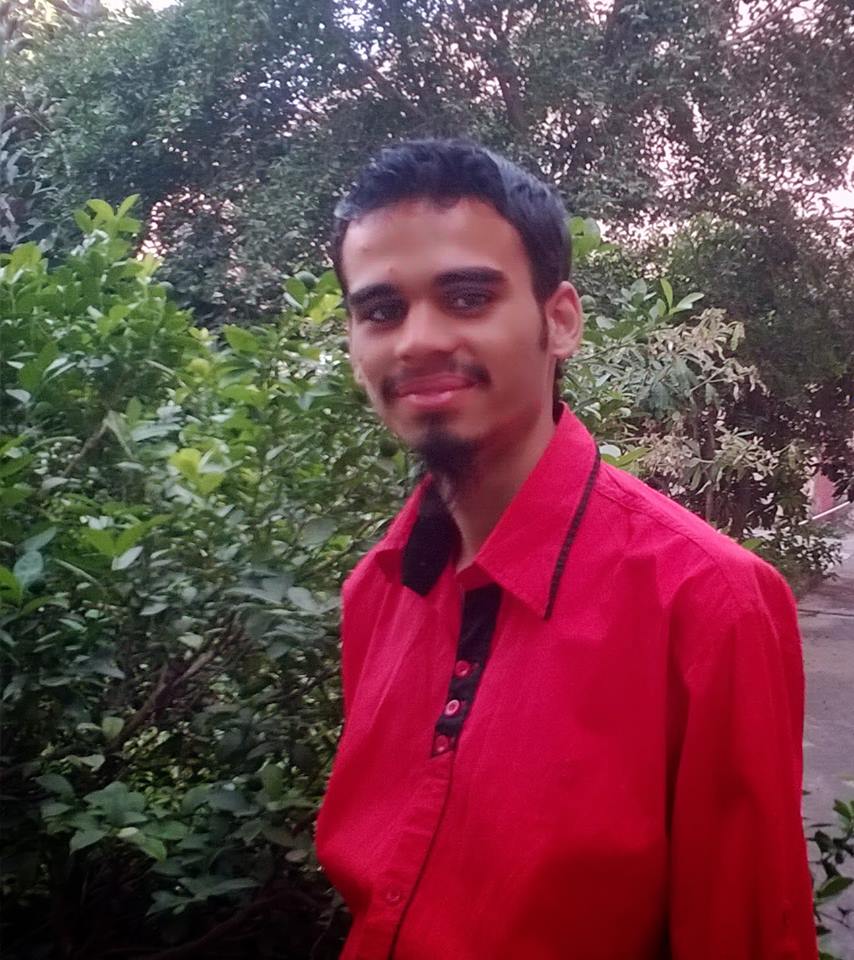
Being associated with art and craft field since decades as a hobbyist and life long learner has given me an opportunity to learn many new things related to art, craft, paints and pottery which i am trying to share with your guys on this website. I have expertise of being professional painter and potter for the last 20+ years
I have learned mind blowing cool tips and insights which makes me a person with ability to improvise and come up with creative ideas and solutions to make stunning and impeccable art pieces of all types which are adored by people across the globe on this website and other platform.