How To Fire Clay Without A Kiln
Making art by hand is more enjoyable and fosters a feeling of connection to the land for both the artist and the art, even if using an electric pottery kiln may be advantageous. A simple technique that may be quickly learned is firing ceramics without a kiln. All you need to heat pottery without a kiln is some fuel and some stones. here we will discuss How To Fire Clay Without A Kiln to dry out the beautiful pottery items made from pottery clay.
Although each clay’s maturation temperature varies, most clays will transform into earthenware pottery at around 700° Celsius or about 1300° Fahrenheit. The temperature of a campfire may reach that level, even though it is substantially higher than a typical home oven, if you are in an area where it is safe and legal to start a fire.
Home pottery-making is gaining popularity. Many individuals start businesses to pursue their interests or to provide unique presents for their loved ones. Burning pottery is one of the most crucial factors to consider while creating it. This article examines a method for roasting clay without a kiln, which isn’t always feasible as building kiln can be costly endeavor for novice to get started with pottery passion.
Ceramics Can Be Safely Fired
Before trying to fire pottery without a kiln, you must determine if you have a secure location. You must have at least 50 feet of clear space free of flammable materials such as grass, weeds, trees, and debris.
To prevent things from getting out of hand when burning pottery, have a spade and a bucket of water close by. A hose’s spray nozzle is preferred over a bucket of water.
Legality is the last element on the list. Is it permissible to light a fire in a city or other densely populated area? If you are unsure, contact your local fire department. Some regions need a permit for open burning.
Raku Firing
Raku firing is a method of heating ceramics. This approach is tough to master and takes great room to obtain the necessary results, even though it yields gorgeous and vibrant ceramic sculptures.
Raku firing needs a big pit area and a bisque or biscuit fire to produce sufficient heat for the pottery to the appropriate temperature.
How Does Raku Work?
A raku fire should be lit outdoors or in a location with enough ventilation. It must be a safe location, away from combustible objects, children, and animals, to start a fire.
The next step is to make a bisque fire, which is the initial firing of pottery before it is glazed. A barrel is often used in Raku firings because it features many apertures through which the heated pottery may be removed.
The pottery must be put carefully in the barrel and positioned close to the fire. The fire should reach between 760 and 980 degrees Celsius in the barrel. The trouble with the Raku method is that it takes a long time to get this temperature since the barrel functions essentially as a kiln.
After the pottery has reached the proper temperature, it must be quickly cooled in cold water or sawdust using tongs and safety gloves. After the glaze has cooled, remove the carbon using a cleaner. The object should then be allowed to dry for many hours before being decorated.
Pit Firing
Pit firing, also known as smoke firing, is a common technique for burning clay. This technique works well for unglazed pottery with a natural appearance, although it may also be used to glaze objects if necessary. As its name indicates, pit firing occurs in a hole or pit.
As with Raku, pit firing requires a well-ventilated place free of other flammable elements. Again, it should be constructed distant from any animals or children who may accidentally fall in.
The downside of pit firing is that it is difficult to maintain a constant temperature. This may lead to an uneven glaze or a more fragile final product.
How does pit firing function?
Like raku, pit firing needs the creation of a fire. It is ideal for digging a hole in a spot that is well-ventilated and shielded from the wind. The temperature of a fire constructed using wood chips, coal, or paper should be between 980 and 1100 degrees Celsius. A charcoal barbeque is a “pit” for specific individuals.
Once the pit fire reaches the required temperatures, the pottery must be cooked for 12 to 24 hours, depending on the desired finish. This depends primarily on whether you choose a natural or glazed finish.
When the finish is satisfactory, and the pottery has formed, remove it with tongs and lay it aside to dry. Alternately, you might dry it in the fire until it completely burns out.
A Kitchen Oven
This is the most stylish way to fire ceramics without a kiln. It is not a good option for ceramic burning on a large or commercial scale, but it is a beautiful alternative for amateurs and hobbyists.
A cooking oven is beautiful introductory equipment since it enables you to experiment and learn new methods before investing in more advanced equipment.
Its most significant drawback is a home oven that cannot achieve the needed temperatures for glazing. Due to the low temperatures, only a few varieties of clay, such as salt dough, may be fired in a household oven, and even then, the end product may be fragile.
What is the procedure for torching pottery in a home oven?
Due to the limited temperature range of kitchen ovens, it is advisable to use clay that can be fired at a low temperature (around 120 degrees Celsius). Place the final piece in the oven for one hour or up to three hours for bigger or thicker crafts. Clay that has been overfired in the stove may become very brittle and stiff.
After the object has cooled, it may be painted immediately with acrylic paint, but it cannot be glazed since the oven cannot reach the appropriate temperatures to keep the glaze in place.
The Outdoor Firing Process
Primary fire
The phrase “basic fire” refers to the first firing of pottery without using a kiln. The primary fire is the first fire used to generate the layer of hot coals that will lie underneath your pottery after it has been fired. As though you were preparing to grill a steak, construct your fire with sufficient quality, long-burning wood to produce a lovely bed of coals. Unlike other hardwoods such as oak, juniper, ash, and mesquite, Pine is unsuitable for making coals.
While your primary fire rages, warm your pottery by placing it near it. At this moment, your objective is to remove any residual moisture from the pots. If the soil is wet, use stoneware or fired pottery instead of green pottery, which may absorb excess moisture. Rotate the pots often to promote even heating. The principal cause of fractured pottery in an outdoor fire is moisture in the clay which can be reduced by prior wedging and little heating of clay.
Kiln Setting
After the primary fire has been reduced to embers, spread the coals beneath each piece of pottery that is being burnt. Place stones over the coals to support the pottery when it is placed there. You may use appropriate kiln furniture if you have it, but many people today still attempt to fire using stones like the ancients.
Consistently, we will refer to these stones as kiln furnishings. This will prevent the pottery from directly touching the burning fuel, which might cause “fire clouds” or black spots. It also facilitates airflow around and under the pottery, which may accelerate the heating and oxidation process.
Using charred pottery, some potters build a barrier between the fuel and the pots. The ancient potters created these slabs of burned ceramics, known as “cover sherds,” from pieces of shattered vessels, but many potters nowadays make clay slabs and fire them precisely for this purpose.
If your pottery is decorated with painted patterns, you may wish to prevent fire clouds since they might damage your artwork. In this situation, you must employ cover sherds to safeguard your vessels. If a vessel is unadorned and unadorned, you may choose to use fire clouds instead of cover sherds.
Atop the ground are hot coals, stones or other kiln furnishings, pots on the rocks, and cover sherds on top of the pots. We may now begin the “secondary fire” or the process of piling wood for our ceramic firing.
Secondary fire
This fire will convert your green pots into earthenware ceramics. If you don’t have enough wood that isn’t much larger than a man’s arm, you must break your large rounds into appropriate proportions. Larger pieces of wood will burn more slowly; the idea is to achieve rapid combustion.
Arrange your wood in a teepee shape over your pottery; angle the sticks so they don’t fall over as the wood burns, but instead rest on the pottery; avoid piling the wood too high. Put on enough wood to provide a sliver of a glimpse of the pottery via a few imperceptible holes. The above images should give you a decent indication of how much wood you will need.
By the time you have finished piling the firewood, the hot coals at the bottom may have already begun to ignite it. Alternatively, little sticks and leaves or lighter fluid might be used. If everything up to this stage has been done correctly, there is nothing left to do except wait for the fire to burn out; it should not need refilling or additional maintenance. The whole fire lasts just 15 to 20 minutes from the start of the secondary fire until the victims are rescued.
Cool down
Those who have never burnt pottery outdoors may be surprised by how quickly the process advances. While a contemporary kiln warms up and cools down gradually to lessen stress, a traditional kiln heats up. It cools down rapidly, subjecting the pottery to significant strain during the fire.
Utilizing appropriate temper (also known as grog) is the key to manufacturing fire-resistant pottery; generally, 20% sand added to natural clay is sufficient.
Your pottery is complete when all the wood has been reduced to charcoal, and there are no longer any active flames. Who isn’t interested to see how the pottery turned out? If required, remove the coals from the pots carefully and slowly to enable them to cool more slowly.
If you used the cover sherds, remove them after a brief time. The pottery is gradually exposed and progressively cooled. Even with leather gloves, holding a pot at this time will leave carbon streaks on your hands from the pot’s surface. Be patient.
You may either wait for the pot to cool or remove it from the fire using a shovel or other non-ignitable metal object.
This concludes the solution to the question, “Can the clay be burned without a kiln?” The answer is “yes.” However, each non-kiln technique for firing pottery has its challenges. This is primarily due to the varying amount of heat produced.
In the case of a household oven, temperature control is limited, and the temperatures are insufficient for the production of glazed ceramics. Raku and Pit Fire methods may be hazardous if not correctly managed, and they may take considerable time to get the desired results.
FAQ
-
Can pottery be produced without a kiln?
You can complete the task. As a result of the misconception that they require a pottery wheel, kiln, or other equipment to create pottery, many individuals may be dissuaded from pursuing this endeavour. In truth, you may produce your first ceramic pieces with nothing more than a lump of clay and your imagination.
-
How is clay fired at home?
One approach is to cook your pieces to 194 degrees Fahrenheit in the oven at home (90C). Bake them at this temperature for 30 to 60 minutes. This will be enough to eliminate any remaining moisture between the clay particles.
-
Can the clay be baked in an oven?
Clay for pottery cannot be fired in an oven since the temperature cannot be increased enough; however, pottery may be fired in an oven, and if you have young children, we recommend this approach.
-
What other option do I have besides using a kiln?
When firing without a kiln, pre-drying your clay pieces in a home oven warmed to 190 degrees F may be beneficial. The pots are dried in a domestic oven by “baking” them for many hours at temperatures below the boiling point of water. The oven was preheated to 190 degrees Fahrenheit.
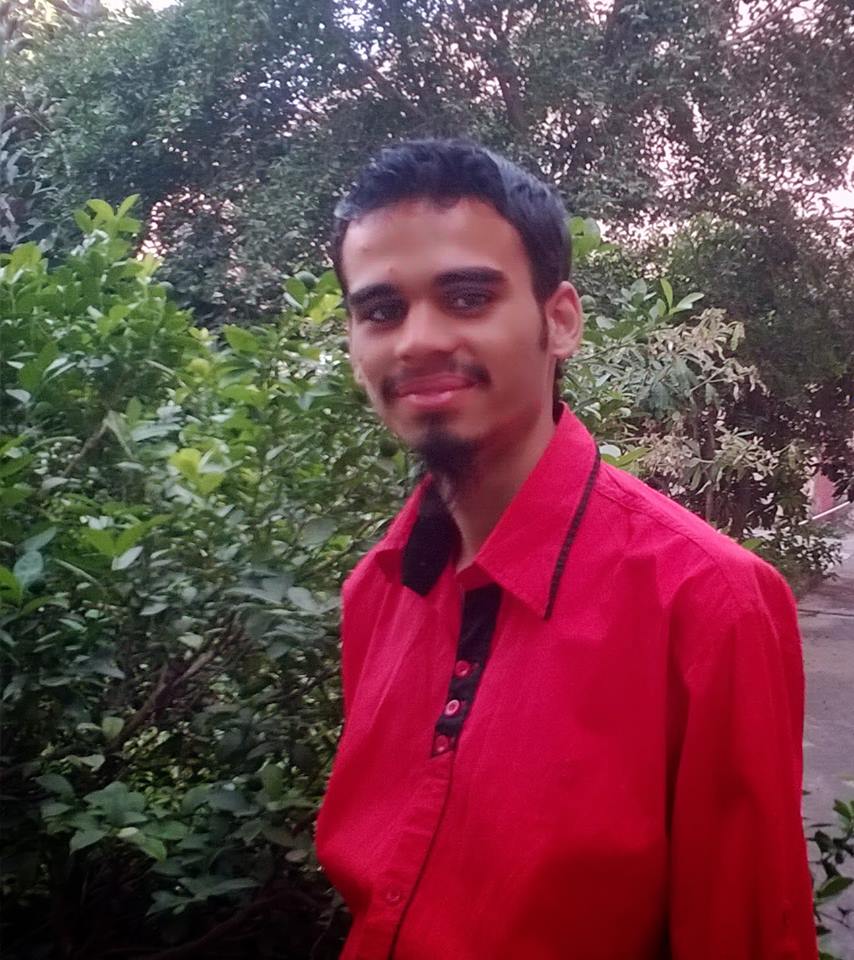
Being associated with art and craft field since decades as a hobbyist and life long learner has given me an opportunity to learn many new things related to art, craft, paints and pottery which i am trying to share with your guys on this website. I have expertise of being professional painter and potter for the last 20+ years
I have learned mind blowing cool tips and insights which makes me a person with ability to improvise and come up with creative ideas and solutions to make stunning and impeccable art pieces of all types which are adored by people across the globe on this website and other platform.