Types of clay for Pottery
Clay is definitely the primary element that constitutes the entire art of pottery. An artist in this field needs to understand various forms of clay and how they behave in different scenarios. here we will discuss more about Types of clay for Pottery for better understanding of clay usage in different objects building.
In ancient times, potters needed to build a spiritual relationship with the earth. There are different kinds of clay that different schools require for pottery. Similarly, different procedures work best for a certain kind of clay but might not be suitable for another.
As a beginner, it is important to know about all kinds of clay that various artists might or might not use. It is noteworthy to have some basic understanding of how each clay is fashioned into its highest potential of pottery.
It is crucial to comprehend why some clay is worth more than others. Therefore, here is a beginner’s guide to different types of clay for pottery making, where they come from, and why they are used.
Clays and inelastic clay are the consequences of deteriorating rocks in which the molecule size is tiny. Most clay contains a few distinct sorts of clay minerals with various measures of metal oxides and natural matter; this separates the various kinds of ceramic clay.
Find out about the various kinds of clay here.
So you’re beginning a stoneware project, yet you don’t know what pottery clay would be ideal. In this article, we’ll cover the 5 distinct sorts of clay for ceramics and pottery.
There are different sorts of ceramic clays accessible in the market. If you’re a novice or aren’t learned about them, you can wind up purchasing some unacceptable clay and burning through your valuable time and cash. Realizing these clay types can assist you with picking the right clay for your next project.
Anyway, what are the four kinds of clay? The four kinds of clay are Pottery clay, Stoneware clay, Ball clay, and Porcelain. Every one of them can be utilized to make ceramics, yet the final product would vary a great deal on account of their various surfaces, varieties, and adaptabilities.
What Is Clay?
Clay is a term for a normally happening soil-like material that is wealthy in aluminum phyllosilicates. The equilibrium of such phyllosilicates close by different mixtures, joined with the states of arrangement and precious stone construction decide the actual sort of clay, which is assembled into kaolin-type (kaolin itself), smectite-type (including montmorillonite) and ilite-type (of which ilite is the main significant model).
Maybe more valuable is gathering clays by their utilization type – which is in a roundabout way connected with their substance and actual organizations. The majority of the clay kinds talked about here are of the kaolin type.
Kaolin
Kaolin otherwise called porcelain clay, or china clay is utilized for the creation of porcelain, with non-clay applications used for papermaking and in the development of plastics. This is predominantly down to its mineral virtue. It is the most flawless clay sort known to man. It is primary clay called essential clay since it is seen as extremely near its source.
Albeit this clay kind has some variety of assortments, they are generally light-hued. They are simply somewhat plastic when contrasted with other clay sorts, making them challenging to work with. Thusly, it is normally blended in with Ball clay to assist with working on its functionality. Two significant shades of kaolin exist, white kaolin and red kaolin. The previous is more normal and is generally utilized as itemized beneath. Red kaolin is comprehensively comparative, except has a red color because of the oxidation of iron oxide.
Asides from having low usefulness, it likewise has a low pliancy level. The unfortunate versatility of kaolin is mostly because of its moderately huge molecule sizes. Thus, pre-fired kaolin pottery can undoubtedly tear when twisted, if in a soggy unfired state (for example dampness levels are poor).
Of all classes of clay, kaolin has the most noteworthy temperature development levels (high-fire clay) with temperatures as high as 1,800 °C. By and large, they are blended in with different clays to increment usefulness as well as lower the firing temperature.
When fired, porcelain can turn out to be exceptionally hard and clear. Likewise, its softened surface turns out to be extremely smooth and sparkling to such an extent that a coating isn’t required. One of the downsides of slender arrangements of porcelain is that it is exceptionally weak and inclined to chipping at the edges – one more justification for why kaolin might be blended in with one more clay to make more sturdy products. Alternately, kaolin is scraped spot-safe in the relieved structure.
Most porcelain things are made of an ideal combination of kaolin and ball clay. Kaolin is generally utilized for the creation of polished paper. It is likewise regularly utilized in the creation of morphine.
How did clay become important to pottery?
What are the benefits of clay over other materials which make it suitable to be used for pottery making? The benefits of clay for pottery making will also help us discern between high-quality clay from its lower versions.
One of the most sustainable materials
Clay is very environmentally sustainable, and it is also budget-friendly. Clay Pottery is available in all places across the world, irrespective of which abandoned Island we are talking about.
The sustainability of clay lies in the fact that it decays to form the very soil from which it is made. This sustainability has made clay an important factor in pottery making.
Natural thermos
Clay pottery act as a natural coolant against environmental heat. In many cultures, certain food items like pickles and even water are preferably only stored in clay materials. Clay pottery or ceramic pottery makes it easier to store food outside refrigerators.
Some pottery is also believed to have antibacterial properties, although that is not really that true.
Optimal for craftwork
Learning artwork on pottery is easy and fun, and often artists create a lifelong spiritual connection with clay artwork on the journey to learning ceramics. Many sculptors also use clay and ceramic pottery as a part of their artwork.
Submits to versatility
Ceramic pottery allows artists to use various techniques in their craftwork. Some Chinese and Japanese pottery on earthenware and porcelain reflect this beauty of versatility which is often associated with pottery making. Historical events can be dated and understood through the nature of pottery making in that period.
-
Very durable
Ceramic pottery is highly durable, making it an easy storage and showpiece material. Clay also does not fade out when color is applied to them, and the effect of dust and dirt is not permanent. Durability is one of the major factors that made clay pottery a household item since the beginning of time.
Clay has great traditional value.
In today’s world, learning to make pottery and using it every day is majorly associated with the traditional value that is a part of what we understand about pottery itself.
As a beginning pottery maker, you will be interested in learning so many historical and traditional artistic styles of creating pottery and how they vary from each other.
Believed to add flavor
In addition to being protective of good, different clay items used as utensils and dinnerware have a reputation for aiding flavor to food. Even though that may not be true, they definitely add a sense of aesthetic that is central only to pottery.
Types of clay for pottery
There are five main types of clay that are widely used worldwide by modern pottery makers. Knowledge of these different types of clay is essential for anyone interested in ceramics.
Sometimes in traditional pottery-making art, various other powders and concoctions were added to the clay to make it smoother, tougher, and more receptive to finer details.
The oldest known ceramic pottery dates from Japan to 10000 BC. It is indeed the home to one of the finest kinds of Asian pottery.
The different kinds of unbelievably simple yet beautiful techniques used by Japanese creators are an important kind of study on their own.
Earthenware clay
For all practical purposes, the display actually refers to the Terracotta clay. Terracotta is a kind of red soil that has been used from time immemorial to create pottery, tools, houses, and even temples worldwide.
They can be glazed quickly or glaze removed easily and have always consisted of the basics of any pottery-making mastery. However, there are many other kinds of earthenware clay as well, which all come in different price ranges. These include the low fire white clay and raku clay.
These clays are usually all low-fire clays which means they are fired at a range of 1479 and 21 09 Fahrenheit. Therefore the firing cone of this kind of clay is 04.
These clays mostly look red or orange and have a huge consistency of iron oxide. That is why they often look like rust. These kinds of clay create porous pottery. They have low results from vitrification.
This kind of clay also has a reputation for breaking more easily in comparison to other forms of ceramic. It is good for everyday use in showpieces and dinnerware.
Stoneware clays
It has a higher firing temperature than its previous option and is named in this manner because of how hard it becomes after the firing process has been completed. This kind of clay is mostly much less porous and has a denser consistency.
The firing cone for this kind of clay is between 4 to 10, which means it fires anywhere between 2010 to 2370 Fahrenheit. These different temperatures mean different techniques can be employed while firing the pottery and, in this manner, employ great quality pottery artwork to create their projects.
Therefore, this means that the firing temperature can be changed according to the will of the pottery maker. The display is one of the most popular places in the market, and it looks like moist and smooth grey to deep gray, slimy surface.
This kind of clay is most widely used commercially in the modern world. It is used for budget to medium-range pottery, and several items can be added to this clay to increase its performance.
In one word, it can be said that this kind of clay is far more functional in a financial sense than its previous option. It can be used to make commercial ceramics, dinnerware and showpieces, jewelry beads, stationery items, and so much more.
They also function as water-holding vessels. However, most traditional households prefer earthenware when it comes to storing drinking water.
Stoneware clays are exceptionally plastic clays. These plastic clays are seldom tracked down in their unadulterated state and are typically hard and strong when fired. They are known as stoneware because of the stone-like attributes they display when they are fired.
Stoneware clays are hard, thick surfaces with a variegated variety. Generally, they are fired to development at a temperature scope of around 1,176 °C and 1,237 °C for mid-fire stoneware clay bodies and around 1,204 °C to 1,224 °C for high-fire stoneware clays.
Stoneware-type clays take on a great many tones when fired. Its varieties range from tan or light dim to chocolate brown or dull dark. These varieties are for the most part impacted by the temperature of the firing utilized.
This clay type is an astounding choice for utilitarian pieces like dinnerware as a result of its hard characteristics. It is thus that it is the go-to clay kind of creation potter. Stoneware bonds fittingly well with its coatings and are typically airtight when fired to development.
It ought to be noticed that stoneware clays are nowhere near uniform – their structure of fire clay, kaolinite, quartz, mica, feldspar, and different minerals can shift fiercely. The kaolinite that might be available will be exceptionally cluttered, with the mica and quartz being available in tiny molecule sizes. Stone might be available.
Stoneware clays are the earliest found kind of clay and are the most normally viewed across the world. Pottery clays are very simple to work with and are profoundly plastic, subsequently are well-known decisions for modern scale creation and craftsman/specialist creation the same.
Dissimilar to kaolin and ball clays, which have just scarcely any mineral contaminations, ceramic contains iron along with different mineral foreign substances that assist the clay with arriving at ideal hardness at lower temperatures.
They are fired to development at a temperature scope of around 951 °C to 1,105 °C. Due to its capacity to be fired to development at lower temperatures, it delivers milder, rather vitrified permeable clay with lively varieties, low psychologist factor and the capacity to be stained without any problem. Ceramics, for example, pottery is unglazed and is normally not watertight or permeable.
It is utilized basically for the creation of tiles, plant items, and bricks. To mend such non-thick fluids, they should be coated. Mechanical strength for this clay sort is normally lower than the others, and consequently, it is framed into thicker articles before restoring.
In any event, when coated, items produced using ceramic are normally less strong than those made of coated stoneware. Pottery clays can be tracked down in their normal states as red, yellow, orange, or light dim. When fired, they typically take on any buff, brown, red, orange, medium dim, or white tone.
Current stoneware clays can be considered compound clays. Regular pottery clay will contain kaolinite (25% by weight), ball clay (25%), quartz (35%), and feldspar (15%). The tones pottery clay takes on when fired normally rely upon the sort of firing and how much mineral pollutants are contained in it. High iron-containing clays will frequently create a redder fired item.
Porcelain clay
Porcelain clay is also known as China clay. This clay comes in the widest range of prices and has a very high firing temperature. This firing temperature begins at cone 9 and goes up to cone 14.
Porcelain clay has always been used worldwide to create high pottery, and few of the most cherished pottery in the collections of the finest collectors belong to this type. This type of clay is often mixed with other ingredients worldwide to give it its characteristic finish.
The display is white or off-white and, after firing, can have a very translucent appearance. This type of clay is non-porous and highly vitreous. It gives the porcelain clay the ability to be impermeable and yet shaped into quite extravagant designs.
In this case, the creator can also use different levels of firing temperatures to give different effects. Pottery makers use this kind of clay to make high-quality products, and artists and creators want to give a striking finish to their sculptural work.
Ball Clay
It is another highly popular clay type normally sold in powder form. However, from its popularity, you might assume that this is a clay type in itself that can be used to produce unique types of pottery. It has never been the case.
Ball Clay, a very popular clay, is usually used as a base for the mixtures added to other kinds of places during their creation. This type of clay is highly plastic and makes any mixture very practical and workable.
It enhances the flexibility and moldability of other clay types and can even be used in highly flexible clays like porcelain to enhance its features further. However, sometimes adding this clay can improve your pottery’s overall quality.
This type of clay is made of extremely fine particles, has a large surface area, and is completely impenetrable. This type of clay is hard to dry and shrinks when it has a surface area that has increased because of the water contracts. Therefore the firing process of this kind of clay is a bit tricky.
This clay type is exceptionally plastic and contains a couple of mineral pollutants. Their tones change contingent on the condition of the material. They are normally dull and dark when wet and light dim when they are fired. The temperature at which they fire to develop hardness isn’t quite so high as porcelain clays at 1,280 °C.
Ball clays frequently can’t be utilized as independent materials because of their inordinate shrinkage that follows during either drying or broiling. In any case, when blended in with different clays like porcelain, they become very valuable as they experience a noticeable improvement in usefulness and versatility. Rheological steadiness is a known component of ball clays, notwithstanding their whitish variety after restoration.
They can be joined with stoneware clays too, which creates a remarkable completed look. Ball clay is exceptionally valued for its utilization in making sanitaryware, ceramics, and wall and floor tiles. Ball clays contain kaolinite (20 – 80% by weight), and mica (10 – 25%) with the equilibrium being quartz sand or other frill minerals. Ball clays are only fine-grained.
Fire clay
Fire clay is just like its predecessor. It is sold in powdered form and increases the firing temperature to a great extent. It means that when this kind of place is added to any mixture, the firing temperature will be somewhere around 2912 Fahrenheit.
Fire clay is refractory clay, which means this type of clay can resist very increased temperatures without distorting. Increasing the firing temperature of any clay type can make the firing process more open to different artwork techniques.
This kind of clay is again never used on its own. Firing clay is also used to make the oven bricks inside the kiln, which again needs to cope with very high temperatures when the pottery itself is being heated.
The main ingredient in fire clay is alumina, a refractory oxide element. It also contains a huge amount of silica, so the temperature at which it will fire rises further.
Fire clay has huge elements and is characterized as recalcitrant clays made out of hydrated silicates of alumina. These clays are known for their especially high alumina content. One of the most conspicuous elements is their high firing range, which is the way the name fire clay was framed.
They arrive at the development stage when they are fired to around 1,480 °C. By and large, they contain no mineral debasements. Notwithstanding, they show a spotted look brought about by spots of iron when fired.
At the point when utilized in mix with stoneware clay bodies, they assist with expanding the development temperature. What’s more, they give the fired stoneware clay a touch of additional harshness.
Fire clay is for the most part utilized for making unmanageable blocks (likewise alluded to as fire blocks) and concrete. Obstinacy is the capacity of a material to endure outrageous temperatures without distorting, breaking, or turning out to be less impervious to compound assault.
Obstinate blocks are utilized in circumstances like in the linings of heaters for metal and glass purifying, and will generally be somewhat thick. Run of the mill present day fire clay blocks are made out of 50 to 60% (by weight) sand/silica, 20 to 30% alumina (coming straightforwardly from the clay) and 2 to 5% lime.
Contingent upon added substances, unmanageable blocks and clay can be probably the most exceptionally performing stubborn materials around.
How to select the correct kind of clay for your project?
Most of the time, the type of pottery you are learning to create will determine what your clay will be using. Sometimes this will be designated by your teacher, while you might find it on the internet at other times. However, a few determinants make any clay type good or bad. Here is what they are.
The pottery type
What kind of pottery you are making will determine the firing cone and the flexibility you require from your clay.
The Clay Type
People usually use four types of clay: Earthenware, stoneware, porcelain, and ball clay. It would help if you chose the accurate type depending on your project. Because each clay comes with various properties, those can also affect the result you want to achieve.
Designs and finishing
Different clay types respond differently to artwork as well as paint. Learning how to carve and paint different kinds of ceramic is highly valuable for a potter.
Budget
Some high-end clay types cost a lot, yet they are essential to certain pottery-making types. Needless to say, your budget will determine your purchase. Additionally, it is recommended for beginners go with lower-priced clay for the practice sessions.
Type of kiln used
Firing kilns are all different and do not yield the same result. If you don’t have a kiln at home, starting cheap and small might be a good idea.
Suppose you own earthenware, a low-fire clay durable at low temperatures, whereas stoneware and porcelain are high-fire clay that needs high temperatures to become durable.
Purpose
Going with earthenware might be the best idea if you aim to create traditional pottery. However, commercial pottery uses at least stoneware.
Conclusion
Pottery making is all about understanding the behavior of your clay. Some of this is a theory, while the most part is clearly a practical experience. Nothing will pre-determine your relationship with the clay and the pottery style which you are going for. if you interested to know why sometimes clay smell different with distinct odour then read about it in this article.
The sort of clay that is decided to work with will be tremendously impacted by the sort of stoneware, block or tile wanted. For instance, while stoneware clay is brilliant for kitchen and supper products as a result of its sturdiness, unglazed pottery clay is an unfortunate decision for such things particularly if the vessel is made to store fluids. Post-firing coating is a famous decision for completing numerous clay types.
Moreover, numerous different added substances can be integrated into pottery – especially those for blocks and tiles (and is nitty-gritty somewhere else on this site). For the best outcome, a mix of at least two clay types might be generally appropriate.
Be that as it may, your care ought to be taken to guarantee the right blend and extent to work out some kind of harmony between pliancy, movability, and strength.
FAQs
Which play has the highest firing cone?
Fire clay has the highest firing temperature and can be mixed with other clay to increase its firing cone as well.
Which clay should you use as a small creator?
You should create stoneware pottery if you are attempting to sell it as a small business.
How much time does clay take to dry?
For the most satisfactory results, you must always use a firing kiln, and clay can take 5 days for earthenware clay to air dry.
What is grog in clay?
Grog is crude, granulated material that is added to clay to make the clay serviceable. Frequently grog is clay that has been fired and afterward ground up into a powder.
Grog can assist with forestalling shrinkage during the drying and firing process. It can likewise be a cradle for your piece from breaking during higher pressure circumstances since grog adds in the middle of between the plastic clay.
Also, ultimately, grog can adds construction to your piece. The grog is like blocks. The remainder of the clay is like mortar. The blocks hold the wall up while the mortar keeps the blocks intact.
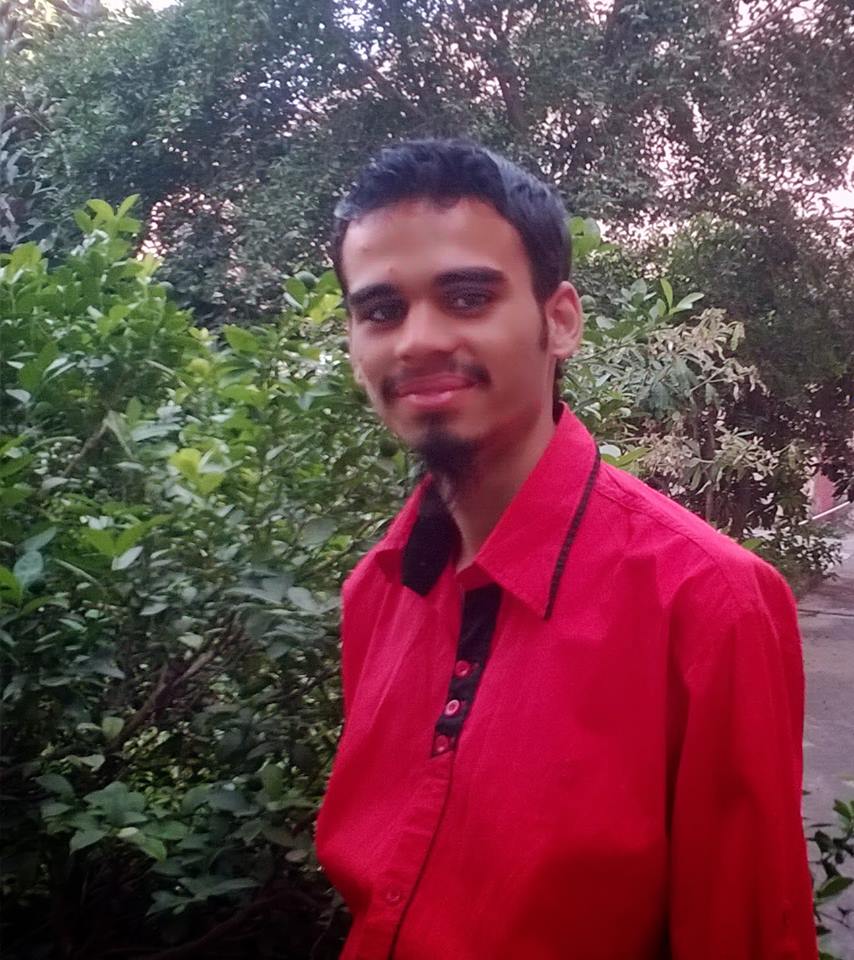
Being associated with art and craft field since decades as a hobbyist and life long learner has given me an opportunity to learn many new things related to art, craft, paints and pottery which i am trying to share with your guys on this website. I have expertise of being professional painter and potter for the last 20+ years
I have learned mind blowing cool tips and insights which makes me a person with ability to improvise and come up with creative ideas and solutions to make stunning and impeccable art pieces of all types which are adored by people across the globe on this website and other platform.