What is the Purpose of Bisque Firing
Bisque Firing will be one of your first words in pottery class or the studio, as it is the most important step of the pottery-making process.
Bisque Firing transforms greenware (unfired bone-dry clay) into a porous and durable ceramic state for the second fire stage. The process enables you to do decorative work on the piece and apply Underglazes and Glazes without damaging or breaking it.
Continue reading to learn more about bisque firing, its purpose and the possible consequences if you skip it during pottery-making.
What is Bisque Firing, and what are its benefits?
Bisque firing is firing clay objects in a kiln at a specific temperature. This temperature is usually around 900degC. Bisque firing has the purpose of strengthening and hardening clay to make it able to handle further processes, such as glaze and glazing firing. The bisque firing process is vital in ceramics because it gives the clay an even matte finish and prepares it for glaze and glazing firing.
Benefits of Bisque Firing
- Strengthens and Hardens Clay: Bisque firing hardens and strengthens clay. This makes it stronger, more durable, and better able to handle further processes like glazing and glaze fire.
- It improves the clay’s appearance: The bisque firing gives it a matte appearance.
- Bisque firing makes glazing easier: The clay is less likely to break down during the glazing process because it’s fired at a higher temperature.
- Bisque firing enhances color: The heat of bisque fire also helps enhance your glaze’s colour.
- Prevents warping: Bisque firing helps prevent warping by strengthening and hardening the clay. This makes it less likely to warp when fired with glaze and glazing.
What is the purpose of bisque firing?
Bisque firing separates bone-dry, unfired clay from its fragile condition. It converts it into a porous, durable state for the second firing stage.
This ancient technique involves transforming greenware (unfired, bone-dry clay) into a porous, durable ceramic material before the second firing stage. This process allows you to decorate the piece without damaging or cracking it. You can also apply Underglazes, Glazes and Underglazes without damaging it. The glazes and decoration adhere to the object perfectly when heated.
The glaze and clay can be damaged if you do not follow the bisque-firing procedure. You can load a kiln very quickly if you follow the instructions. Bifurcated clay, also known as bifurcated raw material, is a raw material fired to increase density and porosity and remove impurities. It can also be used to eliminate organic matter and residual moisture. Glaze firing gives ceramics a bright, artistic finish. Bisque firing can be fun if you practice and master the technique.
The bisque firing is essential for the following:
- The object is transformed from a porous to a glazing state
- You can use stains, glazes and underglazes to decorate the surface.
- The piece becomes stronger without any other work.
- Reduces the chance of damage but if it get broken then you need to read how to repair broken pottery easily.
- Eliminates the possibility of the pot exploding on the second firing
- You should consider adding bisque to your ceramic to make it more durable.
How do you prepare your pottery for bisque firing?
It is important to prepare your pottery properly for bisque firing. Ensure your clay is completely dry before placing it in the kiln. Depending on where you live, it can take anywhere between a couple of days and a few weeks. You can speed up the drying by placing the pottery in a warm and dry area or front of a blower.
Remove any sharp edges or excess clay from the pottery. It is essential to remove these areas, as they can cause the pots to crack or break when fired. Make sure there are no bubbles or air pockets in the clay. This can lead to cracking.
You can then add decorative elements to the pottery. You can add texture by using tools or carving patterns into the clay. Ensure any additional elements are securely adhered to the pottery so they won’t fall during firing.
Before placing your pottery into the kiln, clean it thoroughly. Dirt or debris can cause uneven or discoloured firing. Remove any dust or particles with a soft cloth or brush.
What temperature is best for firing bisque clay?
Bisque firing temperatures are not a precise science. The ideal range for bisque firing is between cone 06 i.e 998 degree Celsius and cone 04 which is 1063 degree Celsius , regardless of the clay or glaze temperature.
You may choose to use a different temperature for a variety of reasons, such as:
- When fired at cone 06, the clay shrinks and becomes porous. It is then easier to glaze.
- The strength and durability of the pots are increased by firing to cone 4.
A higher bisque temperature results in a less porous ceramic. If you want to create a more porous piece that can absorb glaze easily, you should bisque-fire it at a lower heat.
How do you bisque-fire pottery?
The firing process is similar to normal firing but at lower temperatures. Follow these seven steps to bisque pottery:
How to dry your ceramics: To reduce the risk of cracks and explosions, it is important that the clay be bone dry before firing. It can take up to several days for the clay to dry completely.
Choose a kiln: Electric kilns are preferred to fuel-burning ones because they allow for better temperature control and ramp rate.
Set temperature: Bisque firing temperatures range between cone 08 and cone 04 depending on the clay and desired fragility or porosity.
Use the slow ramp rate: Slowly removing water from the clay can avoid cracking or other damage. It is essential to do this at low temperatures. For more information, please see the following section.
Check the kiln regularly: If you hear sounds coming from the kiln, this usually means that the ramp rate is high, and you should reduce the temperature.
Cool down the kiln: After the firing, shut off the heat to let the kiln cool at its own rate. Open the door only when the kilns have reached room temperature. If you cool down your pottery too quickly, it could crack.
If you skip the bisque firing stage, what will happen?
It is technically possible to start the glaze firing without bisque firing. This can be dangerous as ceramics crack or break if not fired correctly. The greenware should also be fired to remove the organic gases and chemically bound water molecules. This can cause glaze or pinholes.
Underglazes and Glazes might not adhere properly to the surface. This will ruin the textures and designs you have created on your object.
If you do not fire glaze and clay slowly enough, the pottery can crack when the bisque process is skipped.
Some moisture remains in the clay because the ware was not fired to the maturity temperature during the bisque firing. Single firing requires slow firing.
Bisque firing ensures that glazes and decorations adhere to the object perfectly.
What is the difference between bisque and glaze firing?
The two firing stages of pottery, bisque and glaze, serve distinct purposes.
The first firing stage occurs after the greenware is shaped and dried. The temperature gradually rises in the kiln until the clay hardens and the chemically bound water molecules and organic gasses are removed. The result is bisque, which is hard, porous and water-resistant. During a separate firing, the bisque ware may be unglazed or glazed in a liquid glaze.
The second firing stage occurs after the bisque has been glazed. The bisque is fired at a temperature higher than the bisque stage. This allows the glaze to melt, fuse and adhere to the bisque ware. It creates a smooth, glossy, decorative, and water-resistant surface.
Bisque and glaze firing differ primarily in the temperature and purpose of the firing. Bisque firing, a lower temperature fire, hardens clay to prepare it for glazing. Glaze firing, a higher-temperature firing, melts and fuses the glaze on the bisque ware, creating an attractive and water-resistant finish.
Sometimes, you might only want to bisque-fire pottery and not glaze it. The bisque firing process can give the pottery a matte finish and make it more porous. This can be beneficial for some types of pottery.
Unglazed bisque-fired ceramics are often used as plant pots because the clay’s porous surface allows water and air to pass through it, encouraging healthy plant growth. You can paint bisque-fired pottery with acrylic or another non-fired finish for decorative purposes without needing to fire a glaze.
Avoid these Common Mistakes When Bisque Firing Pottery
When bisque firing pottery, potters often make a few common mistakes. The most common mistake is not properly drying the clay before firing. When moisture is in the clay, the pots can crack or break.
Unevenly loading the kiln can also lead to uneven heat distribution and a failure to complete the firing. Be sure to space your pottery inside the kiln evenly. This will allow air to circulate between each piece.
The thickness of the pottery is another important factor to consider when firing bisque. Your pottery may not fire or dry evenly if its potteries are too thick. A thin clay can be too fragile and easily breakable. You need to find the perfect balance to achieve a successful bisque firing.
Adherence to the recommended firing schedules for your clay and glaze is essential. A firing too fast or too slow can cause cracks, warping or even an explosion. Refer to the manufacturer’s instructions and make any necessary adjustments based on experience and your kiln.
Troubleshooting tips for common issues during bisque firing
Bisque firing can be problematic even with the best preparation and firing. Overfiring is a common problem, when the pottery is heated too hot or too long. The pottery can warp or get brittle.
Underfiring is another problem when the pottery isn’t fired long enough or at a high enough temperature. The pottery can become porous and weak, which makes it susceptible to breaking and cracking.
Uneven firing can also occur when bisque is fired. This occurs when the potteries are not heated uniformly throughout the kiln. It can lead to uneven color and texture in some areas, as the pottery is not heated evenly.
The type of clay can also affect the result of the bisque-firing. Some clays need a higher temperature for firing than others. Failure to use the correct temperature can lead to issues like cracking or warping.
How do you fire bisque pottery in a conventional oven?
To fire bisque in an oven conventionally, the clay must be low-fire. Regular clay requires higher temperatures than can be provided by a conventional or conventional oven.
Step 1.
Before firing:
- Inspect the bisque piece.
- Check the piece for any cracks or dents.
- Rinse the piece to remove dirt and dust.
This is especially important if it has small wrinkles or holes which could collect dust. Let the piece dry out before you put it in the oven.
Step 2.
Preheat your oven to at least 250 degrees Fahrenheit, and then leave it unoccupied for 10 minutes. You will be able to achieve an even temperature throughout the oven, and it will be ready for firing.
Step 3
Place the bisque piece on the baking sheet and bake it. Assemble the piece in the same position as when finished.
Step 4
Keep the temperature at 250 degrees Fahrenheit. Set the temperature higher to avoid the object cracking because the clay’s water will evaporate too quickly. A lower temperature will not allow the clay to dry properly. This part of the process is more about drying than firing.
Step 5
Let the bisque ware dry thoroughly and correctly. This step will take 25 minutes for thin pieces and 90 minutes if the piece is thick.
Step 6
Close the door and turn off the oven. Allow the bisque to cool down before removing the piece, the baking paper and the tray. To move the tray or the pottery, use oven mitts.
Step 7
Cool the pottery completely by placing it on a flat surface.
Tips to Spot Bisque Items
Bisque is an unglazed white porcelain which is used for dolls and figurines. This is a type of ceramic that has been fired but not glazed. The bisque finish lends the pieces a matte appearance that is smooth and slightly porous. It is important to know how to distinguish bisque from glazed porcelain. Here are some tips to help you identify bisque:
- Color is important. Bisque has a color that is white or off-white and usually has no glaze. The item is more likely to be glazed if it has a shiny finish.
- Feel the surface. The surface of the bisque should be smooth and without a sheen. Glazed porcelain is usually glossy.
- Look for marks. If you see a mark on the item, it will likely have been glazed.
- Check the edges. Bisque pieces have rounded edges, while glazed porcelain items have sharper edges.
Frequently Asked Questions
Why is it called Bisque?
Although the name could be derived directly from Biscay, as in the Bay of Biscay, the crustaceans are definitely bis cuites (by analogy with a biscuit). First, they are lightly sauteed inside their shells before simmering in wine, aromatic ingredients, and cream.
What is the difference between bisque and greenware?
What is the distinction between greenware (or bisque) and greenware? We “pour” greenware by mixing clay and solutions together to create slip clay. Bisque is clay that’s been fired very hot. Then it turns white.
Is Raku required to be bisque-fired?
As usual, bisque-fire your pots. Use Raku-specific clay. Raku artists use glazes to determine when the glaze is ready for reduction. know more about raku pottery in this insightful post.
Can greenware and bisque be fired together?
Firing greenware and glazed ceramics in the same load is considered bad practice. It is common practice and can be done safely. Use glazes and clays that are fired to the same cone temperature. They’ll tell you not to fire bisque and glazed pottery together when they do this.
Can I bisque fire twice?
Bisque firing twice is not harmful to your ceramics. It is common to make bisque fire more than once, especially if you seal underglaze before glazing. Certain decorative techniques, such as china paint, require multiple firings at lower temperatures.
Conclusion
This article gave a good overview of bisque in pottery. Bisque is crucial in pottery-making, allowing for higher quality and more durable finished products. It is essential for those who are just beginning to learn pottery to know the difference between bisque and raw clay and the importance of bisque in the pottery-making process. It is best to practice and research different techniques to perfect the art.
Bisque is a type of pottery fired only once but not glazed. This results in porous clay, which is off-white or lighter-coloured. It is durable enough to be decorated and manipulated. Bisque can be used for decorative purposes or as a base for glazed pottery. Bisque has a velvety, smooth texture. You can also fire it at very high temperatures, and not become brittle.
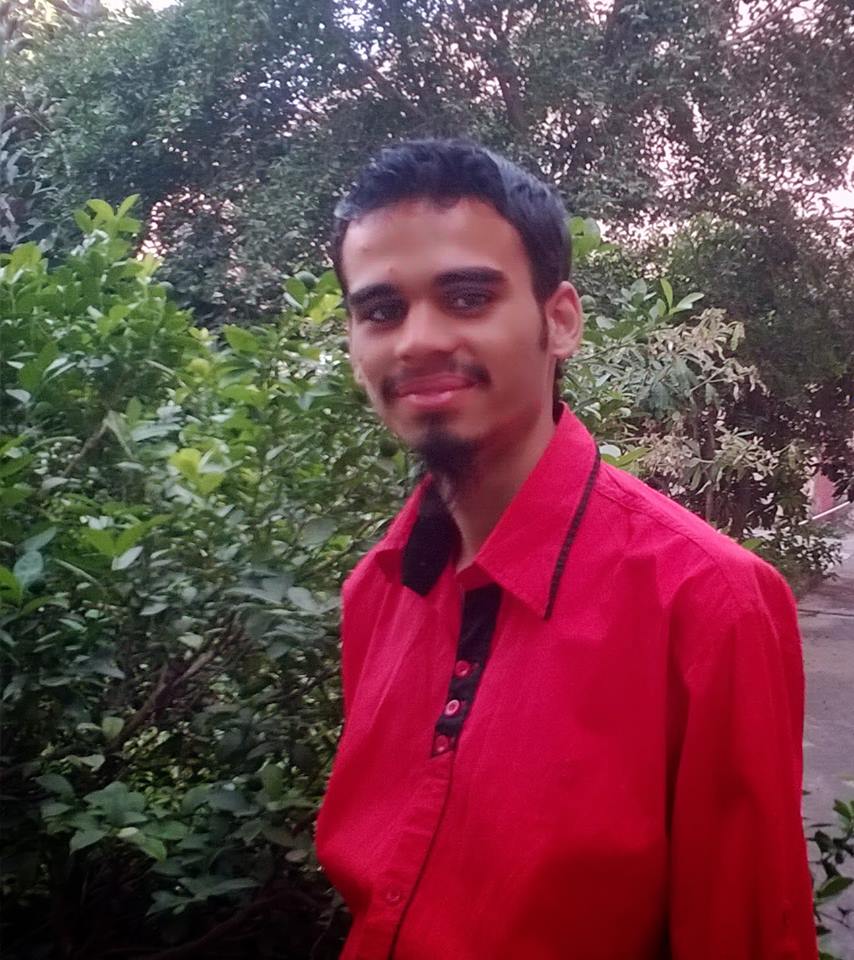
Being associated with art and craft field since decades as a hobbyist and life long learner has given me an opportunity to learn many new things related to art, craft, paints and pottery which i am trying to share with your guys on this website. I have expertise of being professional painter and potter for the last 20+ years
I have learned mind blowing cool tips and insights which makes me a person with ability to improvise and come up with creative ideas and solutions to make stunning and impeccable art pieces of all types which are adored by people across the globe on this website and other platform.